Plastic extrusion for pipes, sections, and custom shapes
Plastic extrusion for pipes, sections, and custom shapes
Blog Article
A Comprehensive Guide to the Process and Advantages of Plastic Extrusion
In the large world of manufacturing, plastic extrusion arises as a necessary and highly effective process. Altering raw plastic into continual profiles, it caters to a variety of markets with its exceptional versatility.
Comprehending the Essentials of Plastic Extrusion
While it may show up facility at very first glimpse, the process of plastic extrusion is essentially easy. The process begins with the feeding of plastic material, in the form of granules, powders, or pellets, into a heated barrel. The designed plastic is after that cooled down, solidified, and cut into preferred sizes, completing the procedure.
The Technical Refine of Plastic Extrusion Explained

Sorts Of Plastic Suitable for Extrusion
The option of the right sort of plastic is a vital facet of the extrusion process. Different plastics use distinct homes, making them extra suited to specific applications. Polyethylene, as an example, is typically made use of as a result of its affordable and very easy formability. It supplies exceptional resistance to chemicals and dampness, making it optimal for products like tubing and containers. In a similar way, polypropylene is another prominent selection as a result of its high melting factor and resistance to fatigue. For even more robust applications, polystyrene and PVC (polyvinyl chloride) are commonly picked for their toughness and durability. Although these are typical choices, the option inevitably relies on the details requirements of the product being produced. Comprehending these plastic kinds can dramatically enhance the extrusion procedure.
Comparing Plastic Extrusion to Various Other Plastic Forming Approaches
Understanding the sorts of plastic appropriate for extrusion leads the method for a wider conversation on exactly how plastic extrusion piles up against other plastic forming methods. These include injection molding, blow molding, and thermoforming. Each approach has its one-of-a-kind uses and benefits. Injection molding, as an example, is outstanding for developing elaborate components, while blow molding is best for hollow objects like bottles. Thermoforming excels at creating superficial or big components. However, plastic extrusion is unrivaled when it involves producing continuous accounts, such as seals, pipelines, and gaskets. It likewise enables a consistent cross-section along the size of the product. Thus, the choice of technique mainly relies on the end-product requirements and specifications.
Secret Advantages of Plastic Extrusion in Manufacturing
In the realm of manufacturing, plastic extrusion supplies several substantial benefits. One significant benefit is the cost-effectiveness of the procedure, which makes it an economically attractive production method. Additionally, this technique provides exceptional product adaptability and enhanced manufacturing rate, consequently boosting general manufacturing efficiency.
Cost-Effective Manufacturing Technique
Plastic extrusion leaps to the leading edge as an affordable manufacturing approach in production. Additionally, plastic extrusion requires less energy than conventional production approaches, adding to reduced operational costs. In general, the economic advantages make plastic extrusion an extremely appealing choice in the manufacturing industry.
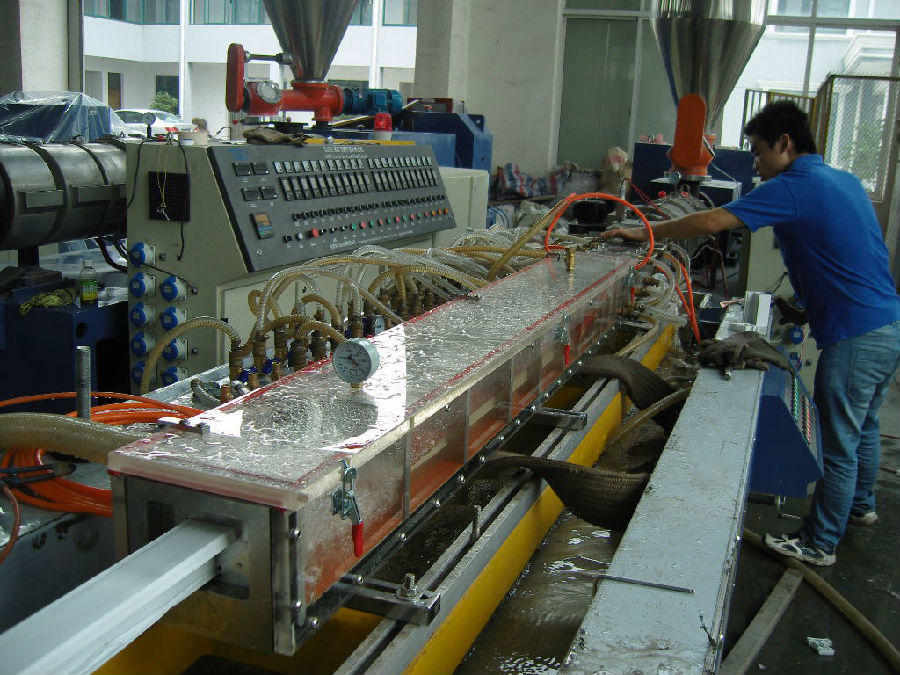
Superior Item Versatility
Beyond the cost-effectiveness of plastic extrusion, another considerable advantage in manufacturing lies in its exceptional item versatility. This makes plastic extrusion an ideal option for markets that call for tailored plastic elements, such as automotive, building, and packaging. In read review essence, plastic extrusion's product flexibility promotes innovation while improving functional performance.
Improved Production Rate
A significant advantage of plastic extrusion hinges on its enhanced production speed. This production process permits high-volume manufacturing in a reasonably short time period. It can creating long, continual plastic accounts, which significantly reduces the manufacturing time. This high-speed production is especially advantageous in sectors where large quantities of plastic parts are required within tight due dates. Couple of various other production processes can match the rate of plastic extrusion. Furthermore, the capacity to keep regular high-speed manufacturing without sacrificing item top quality establishes plastic extrusion aside from other techniques. The boosted production speed, consequently, not only enables manufacturers to satisfy high-demand orders but likewise contributes to increased effectiveness and cost-effectiveness. This useful attribute of plastic extrusion has made it a preferred selection in countless industries.
Real-world Applications and Impacts of Plastic Extrusion
In the realm of manufacturing, the strategy of plastic extrusion holds extensive importance. The financial benefit of plastic extrusion, largely its economical and high-volume output, has transformed manufacturing. The market is constantly aiming for technologies in biodegradable and recyclable materials, indicating a future where the benefits of plastic extrusion can be retained without compromising environmental sustainability.
Conclusion
Finally, plastic extrusion is a efficient and highly efficient method of transforming basic materials right into varied products. It provides various benefits over other plastic forming methods, consisting of cost-effectiveness, high output, minimal waste, and design flexibility. Its impact is profoundly felt in various industries such as building, vehicle, and customer products, making it an essential process in today's manufacturing landscape.
Delving much deeper right into the technical procedure of plastic extrusion, it starts with the selection of the appropriate plastic product. When cooled, the go to the website plastic is reduced into the called for lengths or injury onto reels if the item is a plastic film or sheet - plastic extrusion. Contrasting Plastic Extrusion to Other Plastic Forming Methods
Recognizing the kinds of plastic suitable for extrusion leads the way for a more comprehensive conversation on exactly how plastic extrusion stacks up against various other plastic forming methods. Couple of other production procedures can match the directory rate of plastic extrusion.
Report this page